そるえんす、2001, No.49, 2-22
座談会
近代製塩技術の夜明けU
今日の近代的なイオン交換膜製塩法による低コスト製塩技術が確立するまでの経過を語る座談会「近代製塩技術の夜明け」を2回に分けて企画いたしました。
第1回目(『そるえんす』No.47号に掲載)は、戦後の塩不足時代に国内塩業の振興対策を閣議決定してから、第3次の塩業整備を経て流下式塩田方式と加圧式海水直煮法による製塩体制が確立し、次の時代を担う新しい技術のイオン交換膜製塩法が芽生えて、実用化試験が始まった昭和30年代末頃までを話題にしました。
この度は、その後第4次の塩業整備を経て、2度にわたるオイルショックの洗礼を受けて、現在の製塩技術が確立しました昭和50年代後半までの出来事を話題にして、座談会を進めました。
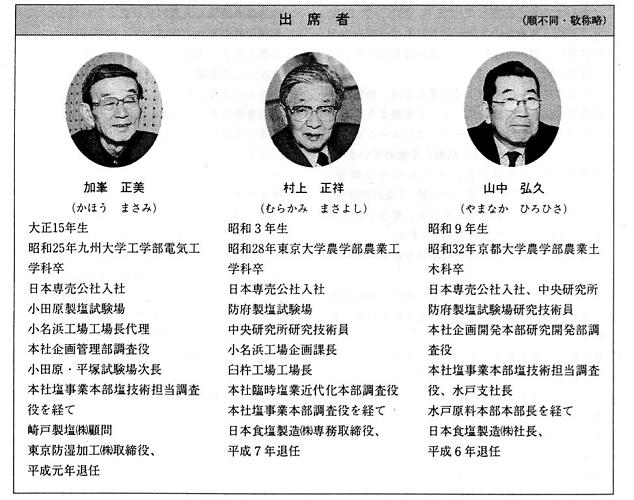
イオン交換膜法の開発研究から実用化試験まで
──小田原試験場での実記試験が協力のかすがいに
司会(橋本) 本日はお忙しいところお集まりいただきまして、ありがとうございます。
第3次の塩業整備後は、塩の技術者、あるいは研究者が、タバコのほうへ少しずつ転換して行った経緯がありました。今日ご出席の山中さんもそのお1人です。第4次の塩業整備前後には、加峯さんも村上さんもタバコのほうへ行かれ、塩事業から離れたわけですが、中東戦争のあおりを受けたオイルショックが起こりまして、今日ご出席のお三方ともに再び塩事業に携わることになり、大変なご苦労をされて現在の技術を仕上げたという、大きな背景があったかと思います。
当時は専売制の下で、専売公社が業界を指導する責任を負っていたわけですが、本題に入ります前に、お三方がその責任者として指導を担当された時期前後のご経歴を、先ずお伺いしたいと思います。
加峯 私は昭和25年に公社に入りました。最初は小田原の製塩試験場勤務でしたが、2年ほどで本社に出て、塩技術課に6年ですか、その後小名浜工場に3年ほどいたわけです。昭和36年に本社に戻ってきて、4年ほど企画管理部(後に技術調査室)にいまして、再び小田原試験場に出て6年程いました。この間はずっと塩でした。第4次塩業整備の段取りがついた昭和46年に、小田原からタバコの平塚製造試験場に1度出て、本社の塩に呼び戻されたのが、(笑)49年です。当時は塩業近代化本部でしたが、昭和51年には塩事業本部の塩技術担当調査役という組織ができて調査役になり、技術体制を整備して技術の改善、指導に当たりました。退職したのは57年です。
村上 私の入社は昭和28年ですが、防府の製塩試験場を振り出しに、東京大井町にあった中央研究所、小名浜の製塩工場と勤務して、そこの店じまいをしたあと、高松の地方局に2年ほど出ました。昭和39年に本社に戻ってきて、第4次塩業整備の段取りにタッチしたわけです。加峯さんがタバコに出られた昭和46年に、私の方は防府製塩試験場の店じまいに出て、その翌年から呼び戻されるまで、タバコ工場勤務でした。呼び戻されたのが、加峯さんより少し後、昭和51年の初めです。57年に加峯さんの後を引き継ぐまで、塩技術担当調査役所属調査役という長い肩書きで……。(笑)公社の退職は59年です。
司会 2カ所の職場の店じまいをしたわけですね。恨まれたでしょう。(笑)
山中 私は昭和32年入社ですが、塩から離れたのが早くて、39年には防府の試験場から岡山の葉たばこ生産試験場に移りました。その後、鹿児島と秦野の葉たばこ試験場に勤務して、イオン交換膜法に転換した昭和47年に本社の技調に来ましたが、塩の担当ではありませんでした。その後昭和54年に、やはり葉たばこ購入関係のジャカルタ事務所に出て、2年ほど海外勤務をした後で、昭和56年にその「所属調査役」で塩に戻されました。それで58年から村上さんの後任として昭和60年3月まで担当しました。ちょうど盛んに行われた燃料転換が終了し、現在の姿になった頃です。その後水戸支社に出されましたので、再び塩から外されました。(笑)60年4月には専売公社が民営化されましたので、公社最後の塩技術担当課長というわけです。会社になってからは、司会の橋本さんが引き継ぎました。
司会 私は本日の司会役ですし、話を専売公社時代までということにしたいと思っておりますが、山中さんの後を引き継ぎましたので、簡単に述べますと、私は昭和38年に入社しました。最初は中研、翌39年には防府の製塩試験場勤務になりました。ちょうどそのときに、先ほどのお話のように山中さんがタバコに転出されるというので、私がその仕事を引き継ぎました。その後、村上さんのお話にあった昭和47年の試験場の閉場までいまして、小田原製塩試験場に移りました。小田原では、仕事の約80%がタバコに転換していましたので、私もそちらの仕事をしていたわけです。それが10年あまりもたった昭和58年に塩に呼び戻されまして、(笑)今度は山中さんの下で仕事をすることになったのです。
山中 その節には、いろいろお世話になりました。(笑)
司会 それでは本題に入りますが、話としましては前と少し重複しますが、新しい技術であるイオン交換膜濃縮法に目を付けたあたりを手短かに話していただいて、それから実用化試験に本格的に入っていくあたりから詳しく話していただければと思います。
加峯 イオン交換膜の研究開発が始まったのは1950年、昭和25年頃からです。私が入社した頃ですから全体の様子はまだ分かりませんでしたが、仕事を進める上で分かってきた範囲で言いますと、初めに特許の問題がありました。アメリカのアイオニクス社が、基本的と思われる特許を出した。それから徳山曹達(現潟gクヤマ)が日本で第1号の特許を出した。それ以来各社の研究開発に拍車がかかったんだろうと思います。当初はいくつもの会社が名乗りを上げていたのですが、だんだん脱落して、海水濃縮用という意味では現在の3社に絞られるわけです。
旭硝子(旭硝子)と徳山曹達はいずれもソーダメーカーで、よく似た点があります。彼らの膜は柔らかくて、陰イオン交換膜と陽イオン交換膜の周辺を貼り合わせて袋を作る。中が濃縮室になり、かん水の取り出し管が付いている。これをユニットセルと言いますが、それをたくさん組み込んで並べた電槽、いわゆる水槽型の方向にいくわけです。一方、旭化成(旭化成工業)の方は、イオン交換樹脂のブロックをセルロイドのように切削して作る硬い膜で、このほうはフィルタープレスのような形に陰膜陽膜を交互に重ねて組み上げた、いわゆる締付型の方向にいくわけです。
司会 その頃、専売のほうも研究に取りかかったと思うのですが、そのあたりは村上さん、どうでしたか。
村上 私は、たまたま事情があって、そのイオン交換膜法の開発のときから総まくりで、資料を整理しました。
イオン交換膜法の最初の報文は、今お話のあったアイオニクスのジュダ(Ionics社、W.Juda「Chemical Eng.News」)の報文でした。それが昭和25年に出ているのですが、専売の中研でも、その頃からイオン交換膜に関連する研究を始めています。そして昭和28年5月の日本塩学会(日本海水学会の前身)に一番最初に発表したのは杉さん(杉二郎、当時中央研究所塩研究部長)とか原田さん(原田武夫、当時中央研究所)、要するに専売のグループだと思います。ジュダらが脱塩に使おうとしているイオン交換膜を逆に使って海水濃縮ができるのではないかという訳です。
その後を追いかけて翌年頃に、岡俊平先生(当時東京大学工学部教授)がジュダの報文を、「イオン交換膜を使った海水濃縮」というタイトルで塩学会誌に紹介しています。それらが、いわゆるイオン交換膜関係の情報がオープンになった最初の頃の情況だろうと思います。しかし、その頃今の膜メーカーも、既に膜の研究を独自に25年から27年頃にかけて始めていますから、どこが最初かということになると問題があります。
昭和31年になって、一番最初にそれを実用化しかけたのは徳山曹達だったわけです。徳山曹達が縮合系の樹脂膜を使って、塩にして1万トンの設備を作ったけれども、結果的にはうまくいかなかった。その後を追いかけて出てきたのが旭硝子であり、それから旭化成が出てくる。専売も、中研でそれまでやっていた研究を小田原で拡大して、本格的に試験を始めています。昭和30年代になると、そういった話はかなりオープンになって、学会でも扱われています。
専売では、イオン交換樹脂を粉末にして作ったいわゆる不均質膜で試験をしていましたが、いろいろ問題もあり将来性もないので、均質膜の方を手がけました。ところが、塩の研究者に有機合成の専門家がいなかったことと、素材の選択が適切ではなかったことなどもあって、結局専売では、膜の合成製造をしないで、装置とか運転技術の方に研究の重点を持っていったわけです。
司会 私が中研に配属になった頃には均質膜の研究に移っていたわけですね。まだイオン交換膜を中研で扱っていて、不均質膜でまだ続けていたのではないかと思うのですが……。
加峯 昭和38年だと均質膜へ移っていたと思います。というのは、前回の座談会で、神原先生(神原周)と稲川さん(稲川徹、当時防府試験場場長)と緒方さん(緒方英世、当時中央研究所第八部長)の3人が外国へ調査に行かれた話がありました。その目的の一つが、実は均質膜を作るための原料の選定だったのです。ですから30何年代になりますと、きっとそれは均質膜へいっていたと思うんです。私が本社の企画管理部にいたときに、小型の試作品ができていましたから。
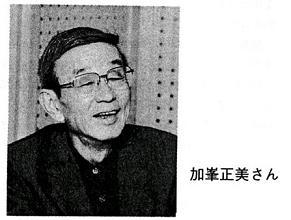
村上 その頃の膜の作り方を見ると、旭硝子と徳山曹達は、布を芯材としてそれに樹脂を塗って、膜に仕上げるという方法でした。ところが旭化成は、もともとセルロイドを作っていたから、その手法で樹脂のブロックを作って、それをスライスする。それで厚さ0点何ミリの樹脂膜を削り出した。だからそれぞれ、会社の持ち味が出ていました。
それから、専売は、どちらかというと初めは、海水を濃縮してそれをソーダの原料にしようという方向にウエイトが向いていたように思います。先ほどの原田さんの報文は、そのほうが主だったようです。ところがソーダメーカーのほうは、逆にとてもそこまではやれないと思って、彼らは塩を作るほうに初めから向かったように、私は思います。
山中 考え方としては、今に通じていますね。
村上 それで、昭和32年10月の衆議院大蔵委員会で、旭化成の当時イオン交換膜開発担当の常務だった宮崎輝さんが、イオン交換膜製塩の工業化設備を導入するという話をぶち上げています。
司会 まだ、第3次塩業整備の前ですね。
村上 そうです。その方針が承認されたのは第3次塩業整備のときです。実用化の口火を切ったのは、旭硝子の膜と設備で日化塩(日本化学塩業)。1万トンの塩量を生産力に織り込んで日化塩が認可されました。それまで旭化成が新日本化学工業(現新日本ソルト)で海水直煮による製塩の生産枠に、佐世保塩業の生産枠を取り込んで、新日本に旭化成の設備を導入することが塩業整備に絡んで決定されています。新日本のイオン交換膜法設備(5万トン)は昭和37年2月に完成しています。これは海水直煮を全面的に切り替えたものです。
山中 私が塩から出る前に実用化試験を経て本格生産が始まっていたわけですね。
村上 ええ。それから、第3次の塩業整備で議論の末にできた錦海塩業が長雨災害等(昭和38年)もあって、どうしても生産量を達成できない状況のとき、3番手の徳山曹達が新しい膜を開発し性能をあげてきていましたので、5,000トン規模のイオンプラントを持ち込みました。こうして膜メーカー3社の設備が、それぞれ出揃ったけれども、それからがまた苦労の始まりだったのです。(笑)
司会 実用化試験に取り組んで、生産枠もイオン交換膜で確保して、運転が始まったけれども、なかなかうまくいかなかったのですか?
村上 収納限度量ということで、生産枠をビシッと決めていたんです。限度量を超える企業もありまして、それには歯止めがありますが、未達のところは格好がつきません。
司会 先ほどのお話に戻りますが、中研のほうでイオン交換膜の開発はあきらめて装置試験を小田原で、実機規模の大きな装置でされたのですね。
加峯 企画管理部にいるときに、稲川さんから話があって、3社に交渉をして装置を入れてもらったわけです。まだそのときは旭硝子と徳山曹達は水槽型で、旭化成は当然締付型です。それを小田原に入れて運転をしたわけです。そのときに海水の前処理については、堺さんが前回の座談会で話しておられたように、日化塩のトラブルなどがあったものだから、既に砂濾過海水をフィードするというようになっていました。
小田原では、畦地さん(畦地昭二、当時小田原製塩試験場研究室長)が試験をきちんとやっていましたから、やがて膜メーカーの人たちも小田原に来て、彼の意見を開くようになって、いろいろ改善のヒントを得たと思います。例えば電極だとか、あるいはスペーサーとか、そのあたりを改善するヒントを、彼らは得たのではないかと思います。
司会 加峯さんが本社から小田原に行かれたのは、その装置が入った後ですね。
加峯 そうです。装置試験のほうは、まあ任せておけばよかったんだけれども、どうも膜も装置も他人のものをただ運転するだけというのは嫌だったものだから、私自身は何か公社独自の技術を開発できないかなというように考えていったわけです。
司会 海水の流れる様子だとか電流分布、あるいは漏洩電流を調べることも、随分されたのではないんですか。
加峯 ええ。それは畦地さんが全部やったんです。ああいう凡帳面な人ですからね。
司会 膜の間に入れるスペーサーも選択されたとか。
加峯 斜交網を選んで潮道から入ってくる海水の分散具合を調べたのです。
司会 うまく乱流で混合しながら、狭いスペースを均一に流れるように、適正なスペーサーを挟み込むことを考えた。それまでもスペーサーは、組み込まれていたんでしょうけれどね。
加峯 スペーサーそのものはあったけれども、液の流れまでよくするという配慮は足りなかったのではないですか。畦地さんが何かモノを見つけてきて、これが良いぞというようなことを言った。それが膜メーカーにも改善のヒントになったんだろうと思います。
村上 話は少し遡りますが、いわゆる海水の前処理。今では当たり前になっているけど、当初はほとんどの膜メーカーは気にしていなかった。というのは、試験にはきれいな海水をくみ上げて使っていたからです。ところが、汲み上げた海水をそのまま使った日化塩で設備の稼働を始めたところ、すぐにトラブルを起こした。すぐ目詰まりするし、それに伴って膜を破損する重大な問題も出てきた。それで海水の前処理つまり砂濾過をまず入れてやるようになりました。
工業原料はそれなりの処理をして、良い性質の原料を使うべきだ。稲川さんあたりが要するに原料に金をかけろと指導した。
司会 前処理をしないと、結局膜間の狭い水路に懸濁物が詰まる。
村上 そう。要するに懸濁物はトラブルの原因。実際には懸濁物だけではない場合もありました。例えば旭硝子は房総の地下かん水で試験をしていた。その地下かん水にはカルシウムがなかったのでスケール問題は出なかった。それを坂出へ持ち込んだら、途端に懸濁物が装置の中に詰まってしまい、電気抵抗は上がるし水分解を起こす。膜の中にもスケールが析出してボロボロに破れ、かん水の濃度は上がらない。
司会 懸濁物やスケール成分がない地下かん水で試験をしてきたけれども、現地の海水にはスケール成分が随分あって、それに伴う問題が浮かび上がってきたということですね。
加峯 日化塩で目詰まりから水分解を起こしてpHがアルカリサイドになった透析槽を解体すると、石こうスケールや水酸化マグネシウムの沈澱がべったりと詰まっており、膜を持ち上げて見ると樹脂が芯材からはがれて簾みたいに光が通ってくるんです。
村上 旭化成の場合も、延岡の試験ではきれいな海水が供給されていた。ところが実際に小名浜工場では、波が打ち寄せれば海水が濁る。そのほかいろいろな問題が出てきたので、海水を港の岸壁から取り入れるように変更した。それから砂渡過装置も付けるようにしたんです。
司会 そうやって、前処理装置を導入して、だんだんうまくいくようになってきた。
村上 あの頃には、その当時の小田原試験場での研究成果が、やはり効いているわけですね。
司会 設備をうまく稼働させるという面で大変な貢献をした。そういう技術がないことには、膜だけできても安定運転できませんから。
村上 当時、新日本では同じようにスケール問題も出ていた。膜の中に石膏スケールが出たんですね。装置を解体して膜を見てスケールの出ている部分を雲に見立てて全面濁っておれば、「雲量10」と言う。それでスケールを出さないようにするために極性転換とかPB法を試みた。
加峯 そこらのところは川手さんが『そるえんす』(No.37)に書かれた記事に出ていますね。
村上 極性転換というのは、今にして思えば、プラスとマイナスを一気に変えるんだから、少々乱暴な話ですね。膜の中へ入ったものが、電流の方向を変えたら膜から出てくるというアイディアなんだけれども……。
加峯 蛮勇を奮ったんですな。(笑)
村上 それからPB法といいましたっけ?
加峯 P塔とB塔とかいって、そこの中でスケール成分を除去するわけなんです。
村上 そうすると、膜の中にはスケールが出ない。そのために、別にカルシウム処理装置をその前に付ける。要するにこれは、膜が悪いのではなくて海水が悪いということにした。
加峯 透析装置が安定稼働できるようになるまでのつなぎに、現場は随分苦労したんだと思います。
村上 それで、スケール成分となる2価イオンをもう少し通さないような選択性の良い膜にということで、新膜の開発に入っていく。それが出そろったのが昭和43年頃の段階だったと思います。
司会 43年頃には、できるだけ1価イオンだけを通すように選択性を付与された膜が出てきていたんですか。
村上 旭化成が、その辺では先陣を切っていたと思います。
加峯 私の記憶では、40年に小田原に着任したときには、小田原の装置に組み込んでいた陰イオン交換膜のほうは、もう硫酸イオンがほとんど通らなくなっていたように思います。だから導入当初の最大トラブルであった石膏スケールの問題は、えらい苦労をしたんでしょうけれど、もう片付いていたと思います。ただし陽イオン交換膜のほうに選択性を与えることは、それ以上に難しかったのでしょう。だから何らかのスケール防止法を開発しなければいけなかったということですね。結局2価陽イオンはパスしますから、炭酸カルシウム・水酸化マグネシウムのスケールは濃縮膜面に付くわけです。それで連続運転が阻害される。そういう状況になっていたと思います。
山中 それで小田原で、スケール防止対策の開発をされたんですか。
加峯 そうです。当時水槽型では、海水に酸を添加してから透析していました。この場合には、出てくる脱塩水は、中和をしてから海に戻す必要があるわけです。それから締付型では、かん水の方も循環していますから、それに縮合リン酸塩を添加する方法をとっていました。
将来的には締付型の方が主流になるという読みもあって、循環するかん水に酸を添加する方法をテストして、うまくいったのです。あれは私がアメリカに出張する前ですから、昭和43年頃です。
なしくずしに進み始めた膜法への転換
──コストダウンには第4次塩業整備の断行が不可欠に
司会 しかし、いろいろな間題を解決しながら第4次塩業整備のとき全面的にイオン交換膜製塩法の採用に踏み切った背景には、なにかデータがあったと思いますが、そのあたりのお話をお願いします?
村上 私は昭和39年10月に、高松から本社の塩業調査課に戻ってきました。そこが塩業審議会の事務局だったのです。ちょうど3社のイオン交換膜工業設備が出揃って、今までの話のようにいろいろと悪戦苦闘している段階でした。
そんなわけで、イオン交換膜法のほうは、まだ初めに見込んだほどの成績が出てこない。そこへもってきて第3次塩業整備のときには、合理化したら塩価は下げられる説明になっていたけれど、長雨災害があったりしてなかなか下げられない状態で、むしろ災害対策で収納価格を上げろという要求が、塩業界からは出てくる。一方、外部からは臨時行政調査会や行政管理委員会などの専売制度についてのいろいろな批判があり、また物価安定政策会議からは塩の輸入などは勝手にやらせろといった要求も出てくるし、もう八方ふさがりの状況でした。
また一方では、新産業都市計画が各地にあって、産業開発が昭和38年頃から盛んになりました。第3次整備の塩田跡地も、多くはそのときに転用されました。その流れの中で、例えば赤穂海水化学工業(赤穂海水)は、塩田を全部売ってイオン交換膜法に切り換える。鳴門(鳴門塩業)も鳴門市の産業開発計画に乗って塩田を売り、その代わりにイオン交換膜法を入れる。収納限度量があるのだから、生産力の補充をイオン交換膜法に切り換えて行うという動きが出てきて、それを専売でも押さえきれない。
司会 しかしこれまでの話ですと、実用化試験でなかなかそこまで踏み切れるほどの成績が出ていなかったようですが、どういうことでイオン交換膜法で第4次塩業整備に踏み切ることになったのでしょうか。
村上 イオン交換膜法がそれほどはかばかしくないとはいっても、例えば新日本はイオン交換膜法
で、5万トンの製造設備を操業しています。それにコスト的には、流下式塩田に代替し得るぐらいの段階までにはいっている。だから流下式の代わりにイオン交換膜の設備を入れるというのは成り立つわけです。
山中 ということ峠、イオン交換膜法に転換してもよい実績が出ていたんですね。
村上 話は遡りますが、塩の生産量の経過を見ると、戦時中から戦後に生産力がガタ落ちになって塩飢きんになった。そこで、塩を作れる者は何としてでも作れというのが自給製塩です。つまり日本の食用塩は大体50万トンから55万トンが必要量だったのに対して、戦後は極端な塩不足だった。それで流下式とか海水直煮といった新技術を具体化して、生産量を戦前の状態に回復したのは、大体昭和28年から29年です。ところが流下式転換がその後もどんどん進んで、生産量は回復を通り越して百数十万トンに達し、過剰になってきた。そこで昭和34、5年に塩田整理をやって、国内生産力を90万トンに抑えたのです。収納限度量が90万トンということです。
その収納限度量の中で昭和40年頃はまだ膜メーカー3社の実用規模装置が出揃ったばかりの段階ですが、それでも塩量にして5万トンか6万トンぐらいの塩をイオン交換膜法で作っています。それが45年頃までの間に増えていくのです。これが今話をしたいわゆる新産業都市計画で、塩田を売却してその代わりにイオン交換膜法を入れて生産力を確保する。当時は「部分導入」という言い方をしていました。
司会 それでは、第4次の塩業整備で一遍に変わったのではなくて、整備までにジワジワと塩田からイオン交換膜法のほうに技術が変わってきて、第4次の整備の直前には、かなりの部分が既にイオン交換膜法になっていたということですか。
村上 今お話ししたように、赤穂海水、鳴門それから崎戸(現ダイヤソルト)も、限度量を満たすために生産力の補強にイオン交換膜法を入れました。そういうことで、昭和45年頃の段階で、もう十数万トンのイオン交換膜法の塩が、現実にはできていたと思います。
その段階でも、膜や装置の改善をみんな一生懸命やっていたんです。43年未だったと私は記憶していますが、新日本から、当時の最新膜での半年ぐらいの試験成績が出てきました。それを見ると、どうやら今度は電気抵抗も上がらないし、かん水濃度も落ちない。これは本物ではないかというような成績でした。そのときのデータを使って、実は私が、自家発電を組み込んだイオン交換膜法の製塩プラントでまとめたらどうなるか、という試算をやりました。規模別の建設費、コスト見積りを出してみたところ、イオン交換膜法で大規模プラントにまとめれば、日本塩業関係者の宿願である、海外からの輸入塩(せんごう塩)に村抗できるようなコストで塩ができそうだという試算結果が出てきたんです。それが44年の初めだったと思います。
その頃には塩田の代わりにイオン交換膜法を入れるという申請が続々出てくるし、それをなし崩しにやっていくと、結局塩の値段は流下式塩田の段階のよりも下げられないということになる。先々のことを考えたら、この際一気にイオン交換膜法に切り換えるべきではないかということになって、第4次塩業整備、塩業近代化に入っていくわけです。
司会 この段階で整理をして試算すると、輸入塩とのコスト競争力が出てくる見通しがついたということで、第4次の塩業整備を、たくさんあった製塩メーカーを規模拡大のために7社に紋り込んでやったということですね。
村上 イオン交換膜法の特徴は、塩田のように広い土地を必要としないので大規模プラントが可能なことです。これによって大幅なコストダウンが見込まれる。コストを下げるためには、流下式塩田や海水直煮等をすべて廃止し、大規模イオン交換膜法プラントに集約して、しかも自家発電とのコジェネでエネルギーを100%利用したプラントにまとめることで、初めてメリットが出てくるのです。
司会 電気透析に使う電力は、自家発電で賄い、発電後の排蒸気をせんごうに使う。
村上 発電後の低圧蒸気を、蒸発缶のエネルギー源に使う。蒸発法としたら真空式より加圧式のほうが理論的にはエネルギー効率が良いけれど、イオン交換膜法のプラントについては、発電との関係があるから加圧式は使えない。それで真空式と組合せました。そのときの蒸気量を発電の蒸気量とバランスさせるようにすると、自家発電単価は買電の約半分になるので、大変なメリットが出てきます。確か最初のプラントは3重効用の真空式だったと思います。そういう一連のフローシートをまとめました。
司会 イオン交換膜法に変えれば大規模に集約することによるコストメリットがあるということですが、その場合には採かんだけではなくて、せんごうのほうも大きく変わり、コストメリットが出てくると思うのですが。
村上 イオン交換膜法に変えるとはいっても、製塩プラント全体を変えることであって、イオン交換膜の透析設備はその一部に過ぎません。だから、いわゆるコストダウンのウエイトからいえば、プラントとしてまとめた透析槽以外のパートのほうが大きいと思います。
その意味で、公社の小名浜工場が大変大きな陰の力になっているんですね。蒸発缶の連続採塩や母液の抜き出しなど、地道な技術開発をやっていた。そういう技術蓄積の上に乗っかって、無洗缶連続運転という手法が成り立っているのです。
司会 イオン交換膜製塩法を組み上げるまでの、いろいろな技術開発の背景としては、イオン交換膜のほうでいえば、膜メーカーは膜性能の向上、装置的には小田原の技術、せんごうのほうでいえば、小名浜の技術が生か.されて、イオン交換膜法に切り換えたときに長期無洗缶で運転できるようになった。そんなことでトータルとしてスケールメリットとコストダウンにつながった、ということですか。 村上 別の側面からいうと、製塩プラントを全部そっくり新設する時でないと新しい技術のメリットを十分に生かすことができない、ということがありますね。例えば、蒸発缶は1度作ったら末代物ですからね。昭和の初めや終戦直後に作った古い製塩工場の平釜とか蒸気利用式などが、第3次の塩業整備で真空式に整理できた。それから今度は、その真空式の蒸発缶をもう少しましな長管式の外側加熱にするとか、連続無洗缶などという技術に合ったようにするためには、従来の鋳物の蒸発缶ではどうしようもない。それが第4次の塩業近代化で新しく設備を作るときに、初めて実現するのですね。
加峯 小田原では装置面のほかに、スケール防止にも寄与しているので、一言付け加えておきます。先ほど締付型装置で循環かん水に酸を添加して、スケール防止に成功したことをお話しましたが、その話の続きです。この酸添加かん水に縮合リン酸塩を添加すると、蒸発缶のスケールも防止できることを、その後発見しました。酸添加したかん水の場合は、高温でもリン酸塩が分解せず、ナトリウムーペンタソルトという複塩スケールの生成を防止できるというのが、その原理です。これは米国出張から帰った後ですから45年頃の発見で、特許になったのは52年です。発明者はアイディアを出した私と研究を実施した杉田さんほかの計4名です。これで採かん工程もせんごう工程も、スケールによって連続運転が阻害される心配は一切なくなりました。透析装置は予想どおり水槽型が締付型に置き換えられましたから、その際杉田博士が業界を指導したわけです。手前味噌になりますが、イオン交換膜製塩の連続運転を可能にした、重要な技術の一つだと思っています。
公社技術陣の解散後に襲ったオイルショック
──再招集に応じて対応のかなめに
司会 それで第4次の塩業整備が行われて、現在の7社が誕生しました。そのときコスト競争力が上がるということで、5年間のスケジュール価格を立てて、毎年目標価格に向かって下げていこうということで、順調な滑り出しをしたわけですね。
加峯 あまり順調でもなかったと思います。(笑)と言いますのは、その後うまくいかなくなった理由を、全部オイルショックによるエネルギー単価の上昇へ持っていくけれども、原単位そのものにも本当は問題があったわけです。
司会 村上さんがまとめられたデータによると、転換したときは、透析電力原単位では塩トンあたり310 kWhぐらい、燃料原単位ですと1,850トンカロリーぐらいですか。そんなレベルで、新しい製塩工場がスタートしたんですね。これで2年ぐらいは塩の収納価格を下げていったけれども、そこへオイルショックが起きた。
村上 オイルショックは本当に青天の霹靂でした。それまでのエネルギー事情と単価の桁が違ったんですから。C重油の値段が、キロリットル当たり5,000円くらいだったかな。
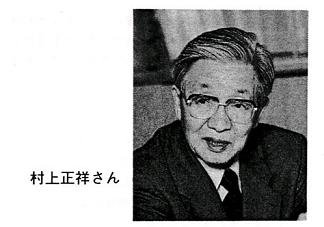
加峯 リッター当たり10円はしなかった。それが、私も村上さんもいなかった第1次ショック(48年)のときに22〜23円ぐらいになって、最後のとどめの第2次(54年)の後では50円位でした。
村上 さっき話したように、私は7社の選定が終わってから、防府製塩試験場の店じまいに出て、それからしばらくは塩業にはタッチしていなかった。本社の塩技術担当調査役に戻されたのは、加峯さんの後でした。
加峯 再召集に応じて。(笑)
司会 第4次の整備が終わって、これで目出度し目出度しで、技術のほうもそんなにフォローはしなくていいということだったのでしょう。塩の研究関係、技術関係者がどんどんタバコのほうに移っていった。村上さんも防府製塩試験場の店じまいをされた後、タバコのほうに変わられた。加峯さんもタバコのほうに変わられた。
それで塩の生産のほうは、専売の技術サポートなしで暫く経過して、この間にコストダウンは少ししたけれども、オイルショックが来てコストダウンができなくなった。しかし専売の技術陣は手薄で、技術改善のようなことは、どうしていいかさっぱり分からなくなってしまった。
加峯 残っていたのは、塩の収納に伴う品質鑑定関係だけでしたからね。
村上 不思議だったのは技術担当の調査役はいたんだよ。
加峯 川添さんと、青木さん(青木司郎、当時塩業近代化本部塩業企画課課長代理)がいました。やがて青木さんも退職され、川添さんだけが残った。技術の残留部隊は、岡さん(岡光蔵、当時塩業企画課課長代理)がキャップで鑑定の人が何人かいたわけです。後で、藤原さん(藤原滋、当時塩業企画課調査役)と西本さん(西本俊雄、当時塩業企画課調査役)が来て、塩業課のほうに所属して仕事をしていた。もっぱら収納価格担当のような感じでしたね。
司会 そういうふうにある程度陣容が固められたところに、加峯さんがキャップとして呼び戻され
た。
加峯 固められたというか、固まってもいなかったと思うけどね。(笑)それで収納価格が上がった
昭和49年に原単位も問題になったわけです。原単位の問題がそもそもあったところへ、オイルショックが追い打ちをかけた。それで収納価格を上げた。川添さんは、何とかしなければいけないと思った。だからといって簡単に人を呼び戻すわけにはいきません。それで困っていたので私と村上さんが忠誠心を発揮して戻ってきたということです。
村上 忠誠心ではなくて。
加峯 強制か。(笑)
村上 ある日ある時、「村上さん、辞令が出ていますよ」と言うので、「誰の?」と言ったら、「あなたの辞令が出ております」と言われました。(笑)
司会 スタートしたときの原単位は高いですね。今だから余計高いように見えるんでしょうけれど。
村上 昭和44年頃の試算は新日本の透析装置の性能をベースにした原単位でした。ところが他の2社は、はっきり言ってそこまではまだ下がっていなかったのです。それともうーつ、それに加えてプラントの中で、電気透析で使う電力と蒸発缶で使う蒸気量のバランスが取れていなかった。例えば、あの頃「放蒸」という言葉が現場で言われていました。「放蒸」というのは、電気が欲しいから発電に必要なだけの蒸気を発電機に流すけれど、蒸発缶ではそんなに必要がない。つまり、蒸気が余るので外へ放出するからコスト高になる。
司会 蒸気を捨てることですか。
村上 そういうことです。それはプラント全体の問題であって、電気透析槽の性能だけの問題ではない。蒸発缶の性能の問題もあるし、それから蒸気、電力バランスの間題もある。いま言ったように、蒸気を全部、100%利用しなければ、それはどこかで捨てざるを得ない。そういう状態で、とにかくプラント全体としたらコスト高を承知で運転せざるを得なかったという状態でした。
コストというのは、例えば塩の歩留まりによってもえらく違う。コストや原単位は生産量で経費や電力量を割るからです。そういうことがいろいろあって、7社がスタートはしてみたものの、そのあたりが分かる人材がまだ育っていなかった。何もイオン交換膜の電気透析法の技術者だけがいなかったわけではなくて、プラント全体を判断できる技術者がいなかったんですね。
司会 それで加峯さん、村上さんを呼び戻し、さらに山中さんを呼び戻した。
村上 極端な言い方をすれば、膜メーカーは、膜の合成やその設備を作ったりはするけれど、塩を作ることについてはよく分かっていない。イオン交換膜を評価する場合も、電力原単位とかん水濃度だけでやっている。
ところがそれでは不十分で、例えばイオン交換膜のほうでかん水濃度を1%上げるのに電力が余計にかかる。しかし、電力を少なくしてかん水濃度は1%低くなっても、蒸発缶のほうで余った蒸気でそれを蒸発させれば同じことになる。要するにプラント全体としてのエネルギーはどうなっているかを見る必要がある。
司会 加峯さんは戻ってこられて、いかがでしたか。
加峯 普通転勤して来たら、座布団はあると思うけれど、座布団は見つけてこいと言われたような感じでした。(笑)実状からいえば、とにかく研究機関のほうはもちろん、本社もガタガタになっていたわけです。地方のほうは鑑定担当だけですから、これでは「コストダウンを検討しろ」と言われても、どこから手を付けていいか分からない。川添さんもその辺は気が付いていたんでしょう。というわけで、声を掛けやすかった私とか村上さんが、突然強制的にですか、(笑)呼び戻されたということではないかと思います。
村上 私はタバコ屋とはいっても工場長ですからね。(笑)別に私がいなくたってタバコはできますから。
加峯 しかし、私はタバコに出ていたのが3年間だったから戻れたんでしょうね。もう少し長くいたら、使い物にならなかったのではないでしょうか。
司会 いろいろと現状把握から始められたと思いますけれども、現状把握もそんなにきちっとはできるような状況でもなかったんでしょうね。
加峯 とにかく猛烈に忙しかったです。早くコストダウンに取り組みたかったんですが、散塩輸送の後始末とか三菱石油(水島精油所)の重油流出事故とか、いろいろ後ろ向きの仕事も多くて。これは村上さんの来る前のことです。
村上 あの時にいた本社のスタッフにしても僅かでしたしね。
加峯 その中でコストダウンの検討をできる人はいなかったですから。村上さんが帰ってきて、やっとできるようになっていくわけです。
コストダウンを目指して必死の体制再構築
──合理化推進に威力を発揮した等エネルギー費線図
司会 それから後、透析電力原単位や燃料原単位が下がってきました。試験研究機関にも研究者が少なくなって、散塩輸送と分析関係ぐらいしか研究していなかったわけですから、後は戻ってこられた方々が、これをどうやって下げてきたか、いろいろ苦労をされたと思います。そのあたりの話をお願いします。
村上 7社の選定のときに、いろいろなイオン製塩プラントのコスト試算をやった責任者が、実は当時担当調査役だった私でした。それで呼び戻されますと、大体あのイオン製塩プラントのコスト試算そのものが少し甘かったのではないか、という声がまず聞こえてきました。それについては、私は決して無理な数字を使ってないという自信はありました。しかし、その頃になると公社の技術陣はコストの内容を全く把握していない。生産量と原価ぐらいしか情報が来ていなかったのではないかと思います。それで、要するにこれだけ金がかかるんだから、収納価格は下げられないというわけです。大体どういう状態で工場が動いているのか、その辺の把握から始めないと判断できない情況でした。
ところが、稼働状況報告を集めて、それから内容を解析し、技術的な検討をするにしても、そのスタッフがいない。(笑)本社はまだしも現地にも試験機関にもそんな人はいない。タバコに変わった人達を戻すわけにもいかないので、今いる人達の再教育と新たに何人かの人を集めるということで、いわゆる塩技術体制整備を図る話になるわけです。
しかしそんな話を本社内部で持ち出しても、「もう要らないといって人を出したのは塩業ではないか。また人を採用するのか」という話ばかりで相手にされない。だから「出された当人がこう言って頭を下げているんだから、人を採用してくれよ」と、口説きまわった。(笑)
加峯 手ごわかったですね。この前の整備のときに塩業職員転出の面倒を見させておいて、舌の根も乾かないうちにまたぞろ何だ、という感じでした。それをやっと修復したということですね。しかし、小田原に分析センターを作る構想などは断念しなければなりませんでした。それで、昭和51年10月に「塩技術担当調査役」という組織が発足した。体制整備とはいっても、それほど大したことができたわけではありません。人の面では新人を若干名採用しただけで、結局われわれ2人が帰ってきたのが最大の補強ですか。その代わり、鑑定担当だった現地の人を全部コストダウンのほうへ向けるために、教育訓練だけは懸命にやったということです。それともうーつ大変だったことは、内田先生(内田俊一、当時東京工業大学学長)が主査をされた塩業審議会の技術小委員会を再開して、技術改善方針をオーソライズしてもらったことです。
こうして技術指導の態勢は次第にできたけれども、それではどんな指導をするかというと、何も手はない。というのは、せんごうは別にして、イオン交換膜法については、昔のような技術的な改善とか指導はできないわけです。それで、とにかく成績の悪いところに、問題点を指摘して改善を求めるという、いとも頼りない方法しかとれなかったのです。
それでも原単位検討会で決めた当面の目標値は、とにかく52年度中ぐらいに達成できた。それで次の年度は収納価格を引き下げることができた。これに力を得て3カ年の経営改善計画を製塩企業に立てさせた。しかし不幸なことに、54年に第2次のオイルショックが来て、べら棒に重油価格が上がってしまったわけです。原単位のほうは、昭和55年度には近代化計画書の計画値を達成したと思っています。ただ、いくら原単位を改善したといっても、お金のほうから見ると結果的にメリットは出ていないわけです。もちろん何か安いエネルギーはないかと情報収集もやったけれども、この時点では見つからず、結局OPECのなすがままでした。そういう中でただ一つの朗報だったのが、旭硝子の新膜・新電槽の開発でした。
司会 電気透析とせんごうの組み合わせで、総合的に評価する尺度という意味では、等エネルギー費線図という尺度でコストメリットが一目瞭然で分かる図を作られましたね。その図に過去の事績や各企業の現状をプロットし、将来どのあたりを目標にしていくかを考える上で、非常に役に立ったと思いますが。
加峯 そこのところを端折って言いますと、旭硝子がアメリカのコロラド川の脱塩計画に応札するつもりで性能の良い大型電槽を53年に開発した。54年にそれをナイカイ(ナイカイ塩業)と崎戸に試験電槽として1槽ずつ入れました。非常に成績がよかったから、ほかの膜メーカーにも頑張ってもらおうと思って話をしたら、徳山曹達はすぐ研究体制を強化しますと返事が来たけれども、旭化成は何も言ってこなかった。それで何か良い智恵がないかと思案していたら、実は村上さんが考案した等エネルギー費線図に気付いた。
村上 私が戻ってきたときには、オイルショックで計画時とエネルギー事情が全く変わっていたので、コスト試算の前提条件が違っている。そのような状況でコストダウンしていくには、まず膜にしても電槽にしても、省エネルギー型でなければならない。ここであえて透析電力原単位の小さい膜や装置と言われなかったのは、さっき言ったように製塩プラントをトータルとして見なければならないからです。
第4次近代化の段階では、イオン交換膜法のトップを走っていたのは旭化成でした。ですから私は、その性能を試算のベースに使ったわけです。ほかの2社はいささか遅れていました。ところがそれから後、旭硝子はコロラド川計画に関連して、一生懸命大型の新電槽や新膜の開発を進め、徳山曹達も新膜の開発をして、省エネ型の電槽を出してきたけれど、旭化成はトップ意識が頭から抜けない。そういう中で改善を進めるためには、具体的な数値で指摘しないといけない。その材料に便つたのが、等エネルギー費線図です。
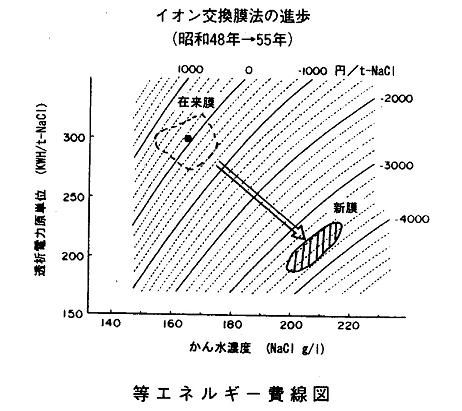
司会 運転成績をこの等エネルギー費線図にプロットすると、その工場なり電槽なりの優劣が一目で分かってしまいますね。
村上 そうです。電気透析だけではなくて、例えば蒸発缶の管理が不手際で、鉄さび等々でガタガタになっていると、それが製塩量に響いて、製塩量が少なくなる。そうなると塩のコストとしては、いくら膜は良いんですと言ったって、トータルのコストとしてはそれはよくない。そういったものをひっくるめて全部一緒にしているのが、この等エネルギー費線図です。透析電力原単位は生産塩量で割った数値だからです。早い話が、塩の歩留まりが5%悪くなれば、コストは5%アップしますからね。
加峯 昭和55年の日本海水学会の研修会のときに、「イオン交換膜製塩の現状」ということで話をしたのですが、その中でこの等エネルギー費線図を紹介しました。受講者の皆さんは、いわば「通信簿」ということで、(笑)熱心に見ていました。先ほどの話で、初期の頃にはトップを走っていた工場がビリになっている。後で聞いた話ですが、膜の開発者でもあった親会社の副社長が、現地に行ってハッパをかけたそうです。
司会 使う燃料ですが、それまではC重油を使っていたけれども、これも高い燃料から安い燃料へと転換していったのでしょう。
村上 オイルショックで痛めつけられている元は、要するに石油価格が上がっているからです。それだったら、石油離れをしたらいいではないかという単純な発想です。その頃具体的にあったのは、海外からの輸入石炭。豪州炭などはかなり割安で手に入る。だから石炭に戻ろうと考えました。しかし昔風の石炭ボイラーではなく、微粉炭燃焼とか流動床ボイラーにする。それから石油蒸留残査のピッチコークスもありましたね。要するに燃料転換をやろうではないかと考えたわけです。
司会 ピッチコークスとかディレードコークスとか、燃料が3種類ぐらいあって、どれを選ぶかはそれぞれ企業の判断ですね。
村上 後は、製塩プラント全体として、蒸気が余ったから捨てるとか、そんなばかばかしいことはしないで、きちんと燃料を100%利用できるプラントに直そうと考え、その段階で標準にしていた3重効用を4重効用にするとか、プラント全体としての省エネ合理化をやりました。
それから買電原単位というのがあって、要するにこれは、蒸気と電気のバランスが取れていなくて発電量不足になっているところを買電で賄っていましたが、それをとにかく減らして、塩トンあたり120 kwhぐらいあったのを70から80 kwhぐらいにまでした。理想的には通常運転では買電はゼロで、運転を始めるときだけ買電を使うようにすればよい。
司会 せんごう用の蒸気と採かん用の電力をバランスさせて、買電ゼロで運転するのが一番いいわけですね。
村上 製塩メーカーも手慣れてきたら、例えば電気透析の電力負荷をバランスするような状態に電流を絞る。それで買電はしない、蒸気も捨てない、というように自分でコントロールする技術を工場はみんな会得しました。
加峯 石炭の値段は重油と比べて、熱量あたりにするとどれくらい安くなりましたかね。
村上 カロリー単価にすると、7掛けぐらいだったと思いました。
加峯 それは大きいね。
村上 それで、これは塩業審議会の技術部会で、製塩企業の小型ボイラーと火力発電所の大型ボイラーの、エネルギー効率の話が出ました。大型ボイラーの採用によりもう少しコストダウンできる手はあるのではないかと言われましたが、「それは先生、遠います。今の製塩プラントはエネルギーについては100%以上に利用していますから」と言ったことがあります。
火力発電のエネルギー利用率は30数%くらいで、後は全部冷却水で捨てている。電力に変わっているのはそんなものです。ところが製塩プラントでは発電後の低圧蒸気を蒸発缶の熱源に利用するので、エネルギー利用効率はほとんど100%に近い。その上、低圧蒸気は真空蒸発缶で蒸発倍数を3以上に利用するから、プラント全体のエネルギー効率は300%を超えています、と説明したら、技術部会の先生方も、そう言われてみればそうだなと納得されました。
加峯 しかし村上さん、さっきの話で、燃料の単価が3割下がったらすごいよね。原単位は9年かかって15%ぐらいしか下がっていないんではないかと思うんです。そのうち専売の指導がなかった5年間は、ほとんど改善がなかったから実質4年だが、それでも15%しか下がらなかった。だから、それが3割カットされると、その効果は猛烈に大きいですよ。
村上 国会などいろいろなところから、塩業近代化の経済効果はどうか、という質問をよくされました。それでソロバンをはじいて見ましたら、3年ぐらいで経済的に元は取れています。第4次のときは220億円ぐらいの予算を請求した。これは全部がやめたとしての請求で、実際には190数億で塩業整備は終わっているはずです。ですから、その後の収納価格が下がった分や、塩業関係の人が少なくなって費用が少なくなった分などを計算したら、3年ぐらいで190数億円の元は取れていました。収納価格を下げたのが、一番大きいですけどね。
加峯 塩田製塩のままだったら大変。それを免れただけでもよかつたと思ってくれればいいんですが、そうは考えなくて、国際水準価格だけが一人歩きした。
村上 塩田製塩が続いていたら、収納価格はいくらになっているはずですという値を原点にして計算しましたから200億円の元は直ぐ取れました。
加峯 それはもう優に元は取れたと思います。ただ国際水準価格が厳然として残っているのには、まいった。(笑)
司会 これまでは、山中さんのいない時代の話ばかりで、山中さんの出番がなかったのですけれども。(笑)山中さんは塩を出られて、何年ぶりに帰ってこられたのですか。
山中 さっきお話ししたように、昭和39年に出て、引き戻されたのは昭和56年ですから。
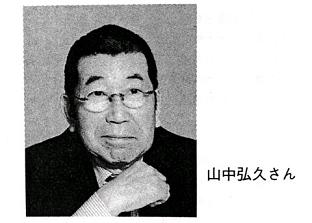
村上 56年といったら、今まで話してきた第4次以後のドサクサの話が大体終わった頃かな。
山中 いろいろなご苦労が終わって、ちょうど新電槽が出かけの頃でした。
村上 燃料転換は、まだ全部は手を打っていなかったでしょう。
山中 ピッチコークス混焼などの最初の燃料転換が検討され始めた頃だったと思います。
司会 どうでしたか。十何年ぶりに帰ってきて。
山中 それは大変でしたよ。
加峯 山中さんと橋本さんには、「本当にご苦労様でした」と言わなければいけないのかな。
山中 いや、「あまりお役に立ちませんで」と言うほうなのでしょうけれども。やはりイオン交換膜法になる前に出ていて、17年振りに帰ってきたら、もう完全にイオン交換膜法になっていましたから、最初はチンプンカンプンのことが多くて大変でした。それでも、研修テキストや技術資料などが良く整備されていたので、何カ月かの間には、どうにか話についていけるようになりました。
司会 防府製塩試験場時代には整理塩田の転用や道路への塩利用、ガスハイドレートによる海水濃縮試験等で、せんごうにもイオン交換膜にも携わっていなかったので、何もかも初めてで本当に大変だったと思います。加峯さんの時代からの引き続きでされていた仕事だと思いますが、何年かごとに企業から出された合理化計画を検討するとか、それから当時は試験研究費を塩価に上積みしていたので、試験研究のヒアリングをしていましたね。
山中 塩技術担当に戻ってきて、印象深かったことの一つは、技術を大きな観点から捉えられていたことでした。先ほどからの話のように、膜の性能にしても、システム全体として見ようとする考え方がとられていましたし、もっと言えば、製塩ということに止まらないで、外界との接点についても、いつも配慮がされていたように思います。
司会 外界との接点といいますと。
山中 話が全く変わるんですけれども、私自身が関わった例で言いますと、イオン交換膜法になってかん水の組成が変わったために、煮つめていくと塩の次に塩化カリウムが析出するので、塩化カリウムを作ろうとすれば容易にできたわけです。
当時スポーツドリンクの普及などで、塩化カリウムが食品添加物に指定されたんですが、その仕様はほとんど日本薬局法をそのまま持ってきたような規格でしたから、製塩由来のものでは精製にコストがかかり過ぎてとても実用の見込みがない。そこで厚生省に実情を話して、その仕様を修正してもらったことがありました。
司会 食品添加物の関係ですね。
山中 その他に、FAO/WHOの食品添加物部会で、食用塩の国際規格を作ろうという動きがあって、通産省を通じて長い間対応が続けられていたのです。その中で、固結防止剤や分析法が日本の実態に合わない方向で決まりそうになったので、オランダで開かれた会議に出席して、意見を述べたこともありました。この間題は、各国にそれぞれの事情もあって、侃々諸々やってもなかなかまとまらなかった。今でも、まだ決まっていないようですね。
加峯 固結防止剤といえば、フェロシアン化ソーダいわゆるYPSを稲川さんがアメリカ土産で紹介されました。わずか数ppm添加するだけで、塩がサラサラになるスグレもので、早速食品添加物の許可をとろうと、厚生省に持ち込みましたが、答えはノー。フェロシアンとシアンは全く別物なのに、シアン=青酸で、消費者の反対に遭うからだめ、というのが理由でした。アメリカでは勿論、他の先進諸国でも食品添加物になっています。私自身もレスリー社に行った時にその偉力を見ていたので、是非許可をとりたいと思ったけれども、どうしてもダメでした。とくに純度の高い塩には、これは絶対に必要なので、いつか誰かに実現して欲しいと思っています。
司会 私も山中さんの2年遅れで呼び戻されて、山中さんの下でお手伝いをしましたが、試験研究のヒアリングとか、改善計画のヒアリングのために出された改善計画を技術的にチェックして、コスト試算なども山中さんがされました。十何年のブランクがある中でそういうことをしなければならなかったので、大変なことだったと思います。
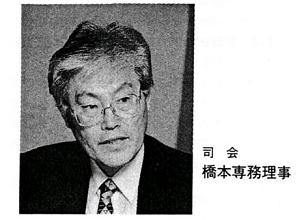
加峯 面倒を見るのが大変だったんでしょうね。それは分かります。
山中 だけど今の試験研究費の話の後、膜がだんだんよくなり、より長期間使用に耐えるようになったこともあって、さらに原単位の下がる膜が実用化されて製塩企業は更新しなくなった。それで、膜の更新を促す補助金を出すようになった。
司会 膜メーカーには、省エネルギーの膜を開発して欲しいという要求を出しても、導入するメリットはというと、例えば先ほどの等エネルギー費線図に乗せて見ますと、更新するメリットがないのです。そうなると開発のインセンティブは働かない、膜メーカーも膜の技術そのものが維持できなくなるということから悩んでいました。
村上 しかし膜メーカーの当初の話では、イオン交換膜というものは前途洋々たるものであって、その機能はほかにもいろいろな応用の分野があるので、製塩用の膜はその一部に過ぎなくなる。だから膜の開発や供給については、ご心配はかけませんというような言い方でした。
しかし考えてみれば、製塩用のイオン交換膜は、初めにセットしてしまえば、その消耗率は年何%とすぐ分かるわけです。それだったら、毎年補充する膜の枚数というのも、立派な膜を作れば作るだけ少なくなる。そうなれば、製塩用のイオン交換膜のプラントを3社がそれぞれ持っているのは、およそ無理なことは分かっています。
初期の頃の意気込みでは、製塩用は一部に過ぎずそれ以外の分野にも進出する前提でスタートをしている。ところが蓋を開けてみると、製塩用の膜は量が多い。ほかの用途では、例えば醤油の脱塩などでも、設備としては知れていて、せいぜい膜が何十枚とか何十対とか、それぐらいの設備で間に合う。それから淡水化のほうにしても、そんなに膜をどんどん消耗するようなものだったら、淡水化が成立しないわけです。
ですから膜事業そのものを、例えば製塩用の膜については1社だけのプラントで共同して作るといったことを、考えるべきではないかと思います。
力を傾注した公社内外への研修・訓練
──業界・学会を巻き込んで多目的に
司会 技術管理だけではなくて、技術員への指導というか研修などもされましたね。加峯さんや村上さんは随分テキストを作って残されました。山中さんの時代にも引き継いでやって、私の時代にも少しやりました。
村上 当時、塩業関係の職員のテキストには、どうもあまりしっかりしたものがなかったのです。試験研究報告などは、ある特定のパートだけで詳しすぎるし。
司会 専売に塩の研究者が大勢いた頃には、製塩企業に対して指導ができる体制が組まれていたからよかったですが、第4次の整備の後には、塩関係の試験研究は分析技術に限られていました。
村上 中研も塩気がほとんど抜けたし、小田原でもだんだん塩気が抜けてね。
司会 そうです。ですからオイルショックの後では、地方にも、分析の分かる人はいたけれども、企業を技術指導するなどいうことは、とてもできるような状況ではなかったと思います。
まずは何人か採用した若い人を育て上げるのに、いろいろなコースを作って訓練されましたね。私も、いきなり先生になれということで、勉強させてもらいました。(笑)
村上 3カ年計画で、新規採用は全国で14人か15人。
加峯 うん、そんなもんでしょうね。
村上 先ほどお話ししたようなことで、まず何人か採用しました。それと在籍していた人も集めて訓練した。その時期には、技術的にはむしろ製塩メーカーのほうがよく知っていて、指導なり文句が言えない情況でした。
加峯 地方に人がいるわけでしょう。それをやはり何か活用することを考えなければ動けませんしね。だからそれは、村上さんがえらい骨を折ってやったんです。セールスエンジニアリング訓練の新しいコースを作って中央研修所でやりましたね。
村上 商品として塩を売るのに、塩についての知識が希薄になっていたからで、あれは良い名前を付けたもんですね。
加峯 えらく高度な内容だと。(笑)
村上 セールスエンジニアを養成する研修を初めて研修所でやりたいと言ったら、所長が「なんですか、それ」と言った。分からないんですね。あの頃セールスエンジニアというのは、初めて出てきたような言葉でした。
加峯 研修所に、ガスバーナーや何かを持ち込んでやったでしょう。
村上 中央研修所に、いわゆる理科の実験室みたいな設備を準備してもらって、商品としての塩を扱う職員の研修をやりました。そのうちに業界の塩工業会(鞄本塩工業会)にも仕組みを作ってもらってやりました。それからもう一つは日本海水学会の研修会。塩を中心にしてやってきたこの学会自体が、ちょうど淡水化の仕事に日が当たっている時期だったこともあって、とにかく「水」ばかりで、塩気が全く利いていない学会になっていました。そこで少し塩気の利いた研修会にしようということで、塩を中心にして、箱根湯本の観光会館で行いました。
加峯 研修会への行きか帰りに、支部局や製塩メーカーの人達が小田原試験場に立ち寄ってくれれば、彼らのほうも刺激を受けるだろうし、試験場にも刺激になるという考えからです。
問われた専売品の品質管理
──管理目標の設定でクレーム激減
司会 塩の作り方が変わってきましたので、塩の品質も若干変わってきたと思います。これまでは製塩技術ということで、採かん、せんごうを中心にしてきましたが、最後に塩の品質について、流下式塩田時代の塩とイオン交換膜法になってからの塩の品質的な違い、ということではどうでしょうか。
村上 海水を蒸発濃縮したものでも、塩田と海水直煮とで違いはあるけれども、イオン交換膜法になってからは、かん水の組成が相当変わってきたので、塩の品質も当然変わってきています。しかしその対策は、全く取られていなかったのです。
一番最初に問題を起こしたのは赤穂海水です。初めて全量イオンかん水に切り換わって操業を始めて暫くしたら、地元赤穂の一般家庭の主婦から、「この塩は味が変です」というクレームが付きました。その報告があって現物が送られて来たので、すぐにそれを調べてみたら、当時の普通の並塩に、塩化カリが2%ぐらい入っていたと思います。
今までの塩田かん水だったら、塩の次に結晶として出てくるのは硫マ(硫酸マグネシウム)で、その硫マが析出する前に母液をブロー(排出)する。ところがイオンかん水になったら、先ほど山中さんからちょっと話が出ましたように、塩の次には塩化カリウムが析出します。このケースでは、おそらく蒸発缶の運転の終わり頃の雑塩回収の段階で、塩化カリの結晶が入ったんだろうと思います。それが最終的に製品のほうに混じったということです。塩化カリでクレームが付いたのは、昭和44年頃のことです。 司会 第4次整備の前ですね。
村上 その次に出てきたのは、紙袋の「濡れ」の問題です。イオンかん水は純塩率も高いし、洗塩なども十分にやりますから、放っておけば純度がどんどん上がる。普通にやれば97%ぐらいの塩はすぐできてしまう。そうすると塩の生産量から見ればその分損をするから、水分の多い塩を出荷する。検査規格からいえば、純度は95%ぐらいあればいい。水分つまり付着母液を多く残すと、溶けている塩マグ(塩化マグネシウム)と塩カル(塩化カルシウム)が多く残る。つまり吸湿性が強いものが母液として残るから、包装袋が吸湿し、これを「濡れ」と称するわけです。並塩の袋がベタッと濡れる。
加峯 粒径が大きくて水分が多いと、袋に水分がにじみ出るのです。極端な場合には、持ち上げるとスポーンと中身が抜けるといったような現象が起こった。
司会 ということは、水分が多くて粒径も大きいと、塩が水分を保持できなくて垂れて袋を滞らし、強度が弱くなる。
加峯 そういうことでしょうね。
村上 粒径のことでいえば、蒸発缶を管内流速の早い外側加熱にしたので、普通に運転したら塩の粒径が大きくなり勝ちです。あの頃は、放っておいたら平均粒径が500ミクロンぐらいの並塩もぎらにあった。560ミクロン近くなることもありました。
司会 随分大きいですね。
加峯 それは公社の粒径規格がおかしくて、幅が広いわけです。どんな企業の製品も合格するようになっていた。粗いのも細かいのもあったということです。
村上 平均粒径で決めていましたね。平均粒径で350ミクロンというのは、確か日本食塩の粒径だったと思います。最初の頃で350以上470ミクロンぐらいまであったかな。そこへもってきて、公社に収納する塩のほかに、販売特例塩といって、メーカーが直接大口ユーザーに売ってもいい制度を導入したのです。それで、販売特例塩で出荷した残りをみんな公社が並塩として収納するから、並塩でも粒子の粗いものがある。その上、そのまま脱水したら品質が良すぎて損をするから、遠心分離機の回転数を落として水分を増やす。その水分が塩マグと塩カルの母液だから、袋が濡れて破れてしまう。それを解決したのは加峯さん。
加峯 袋の滞れは粒径と水分、固結はマグネシウムの濃度と粒径を管理すればよい。公社が買い上げた塩が、マーケットでクレームを起こすのだから、どういう条件で回避できるかを示してやらなければいけない、ということでやったわけです。
司会 クレームの最大のものは塩の固結ですね。
加峯 固結と異物混入と、新しく出てきたのが今村上さんが話した袋の濡れです。これを片付けるのは大変でした。
村上 それを加峯さんがうまく組み合わせて品質管理目標を定めた。
加峯 当時製塩企業は、公社の検査に合格しさえすればいいという風潮だったのです。公社の検査規格は、量目も純度も下限規格だけだったので、企業は上限管理には全く無関心だった。そのために、量目では全メーカーが計量法上の上限違反、純度ではさっきの話で、98%を超える並塩が市場に横行しているといった状態でした。
管理状態の指標である管理係数が1.2以下だと、管理状態が良好というわけですが、当時計算してみたら、3とか4という結果がゾロゾロ出てきたのです。これは何とかしないといけないというので、製塩企業の社長さんに直接話をしたり、一部の工場には現地指導をしたりしました。また管理状態の悪い項目については、検査の合格判定値にペナルティをつけるという強硬手段も取りました。その結果、市場での混乱が無くなったほかに、歩留まりが上がってきたのです。
司会 固結の方はどうですか。
加峯 当時の主なクレームは、さっき話したように、濡れと異物混入と固結でした。異物混入の方は、抜取検査で防ぐことはできません。クレーム情報を流すから自分で解決しなさいということにしました。
それで固結ですが、これまで永年試験研究機関で解決できなかった間題です。試験をしている余裕はないから、在庫塩検査のデータを解析してなんとかしようと考えました。それで、まずハードルを低くしたんです。在庫期間が6カ月以内で、固結強さは平方センチ当たり1キロ未満を固結していないとみなして、紙と鉛筆で整理しましたが、頭のほうは頭痛がするほど使わなければいけなかつたわけです。それから条件の一部などは、今だったらおそらく躊躇するような、大胆な前提条件を置いて解いています。それでいろいろご批判も受けましたが、結果さえ良ければそれで良しとして進めたのです。
するとこれがまたばっちり当たって……。それからは、固結と滞れについては目標値を与えて、これで管理しなさいとやったわけです。その結果異物混入を含めたクレームの発生件数が、昭和49年度は年間70件ぐらい、5日に1件どこかで起こっている計算だった。それが、54年度では年間9件に減っています。その後のことはデータがないけれど、おそらく悪くはなかったろうと思います。私が退職した57年までクレームらしいクレームというのはまず聞かないで済んだということです。
山中 本当に、霊験あらたかだったのではないですか。
加峯 霊験あらたかだったけれども、品質関係は昔からあまり評価してくれないものでね。コストのほうは表面に出るけれども、品質のほうはあまり表面に出ませんから。
「自然塩」の発端は塩田廃止の反発も
──対応は責任ある情報の積極的な提供で
司会 製塩技術の進展に付随して出てきた問題にも、対応に苦労をされたのではないかと思います。その中で、塩の品質という面で、イオン交換膜法に代わってからは自然塩返りの問題も、結構大きな問題ではなかったかと思います。これは、新しい技術の開発で新しい品質になってくると、当然起こるべくして起こったのかも知れません。しかし、塩の品質のどこがどう違って、それがそのような問題になるのかといったことについて話してもらえませんか。
加峯 塩の品質が変わったからということではないように、私は思っています。というのは、その頃、公害に反村する運動が起こっていたでしょう。それで食品についても品質、さらには製法にまで消費者の目が厳しく向けられるようになってきました。そういう所から塩についてもイオン塩有害説が出てきたのではないかと思っています。特に純度が上がったから問題が出てきたというよりはね。
そしてもう一つ言えば、塩業整備で職を失った人の怨みみたいなのもあったように思います。それらが一緒になって出てきたのでしょう。有吉佐和子の『複合汚染』という本の中にも、塩のことが出てくるわけです。すぐき屋六兵衛という京都上鴨神社の近くの漬物屋さんが、「国内塩は有害だから輸入塩を使っています」とか、そういう一節がある。いろいろ叩かれたわけです。
司会 未だに関心が高くて、未だに基本的には解決されていません。そういうことに対してどうやって情報を流すか、ということを考えなければならなかったのではないでしょうか。専売の時代には、聞かれれば答えるけれども、情報を積極的に流すことは、ほとんどしないという姿勢で来たのではないかと思います。
加峯 さっき村上さんが言ったセールスエンジニアリングの研修は、商品知識の他にそういう面も補いたかったわけです。ただ公に対する対応は、現実問題として本社で扱っていました。
村上 自然塩問題の発端は、イオン交換膜法が塩田に取って代わることが現実味を帯びてきた昭和42年から43年頃の段階で、当時、扶桑塩業組合の某氏が、「イオン交換樹脂膜とかいう、有機合成の膜を使って作った塩は危険だ。食用の塩というのは、塩田で作った塩であるべきだ」というようなことを言い出した。つまり、イオン交換膜法によって、塩田が廃止に追い込まれることに対する反発でした。
それから2、3の業者が、イオンかん水でなく、塩田かん水から作る今の塩と同じような塩を作って売りたいといってきた。また、伊豆の大島などでは、海水を使って従来の原始的な方法で作った塩を売りたいという。それは結構ですから、特殊用塩という制度の中で認めることにした。これは専売塩を原料にして、それを加工して商品にする特殊用塩という制度がありますから、それでやって下さいということにした。ただし「自然塩」というのはおかしい。入間が作った塩というのは、決して自然塩ではないので、商品にそういう標示は駄目ということで、45年頃の段階で、全部仕切った筈です。ただ自然塩○○協会という名前は勝手だから、その名前を変えさせることまではやりませんでした。
司会 そうすると、今初めて知ったのですけれども、自然塩問題は昭和47年の整備後に出てきたのではなくて、その何年か前に、イオン交換膜法の塩が工場で作られ始めた頃に始まったんですね。
村上 塩田をつぶしてイオン交換膜法に切り換えようという状況になったときに、塩業者のほうから、自分たちの先祖代々の職を奪うのかという反発の中で、そのような動きが出てきたのです。
司会 しかし、結構高名な先生まで自然塩を有難がっていますね。(笑)
加峯 松山のNHKテレビに出演させられました。そのときの相手が大学の先生お2人です。その次は海水学会でしたが、当時会長さんだった武藤先生(武藤義一、当時東京大学生産技術研究所教授)が裁いて下さいました。その後は、参議院の決算委員会でした。何か勝手なことばかり言われてしまって……。要領が分からないから、こちらは手を挙げて反論させて欲しいという合図をするんですが、委員長は黙殺。イオン製塩では硫酸を入れて塩を作っているとか、日本食塩の漬物塩のほうにも飛び火しましたね。何かムカムカしながら帰ってきたことを覚えています。(笑)
村上 日本食塩は、かん水の精製工程で中和のために塩酸を使っています。だから、塩酸のタンクローリーが日本食塩に入っているというのは、当たり前のはずですが、「塩酸を添加していて、あれは怖い」とか何とか、という話にまで脱線しましてね。
司会 当然食品添加物用の塩酸を使っているんですから、別に問題になる話ではないと思いますけれどね。
自然塩問題については、もう少し話を続けたいところですが、予定の時間も過ぎておりますので、この辺で締めくくりたいと思います。今日はイオン交換膜法の開発から始まり、実用化試験をクリアーし、第4次の塩業整備による全面転換後に見舞われたオイルショックを乗り越えて、現在の製塩技術が確立するまでの経過をお話ししていただきました。お陰さまで日本の製塩技術は進歩して、外国と負けないくらいのコスト競争力があるという整理の下に、平成9年に塩専売制が廃止されました。製塩技術の真価が問われるのはこれからだと思いますけれども、それは後の時代に判定が下されることで、今日は技術開発に伴うたくさんのエピソード、あるいは苦労話をしていただきまして、どうもありがとうございました。これでこの座談会を終わりたいと思います。
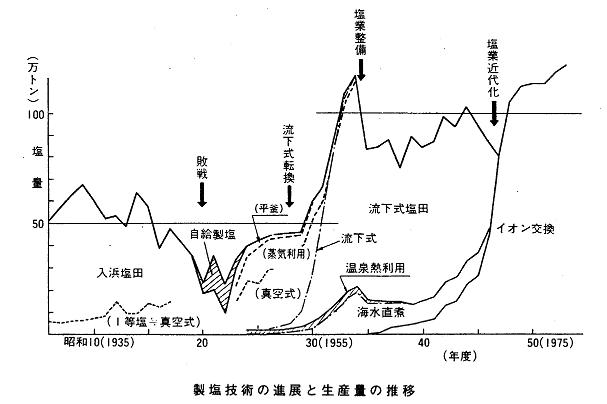
|